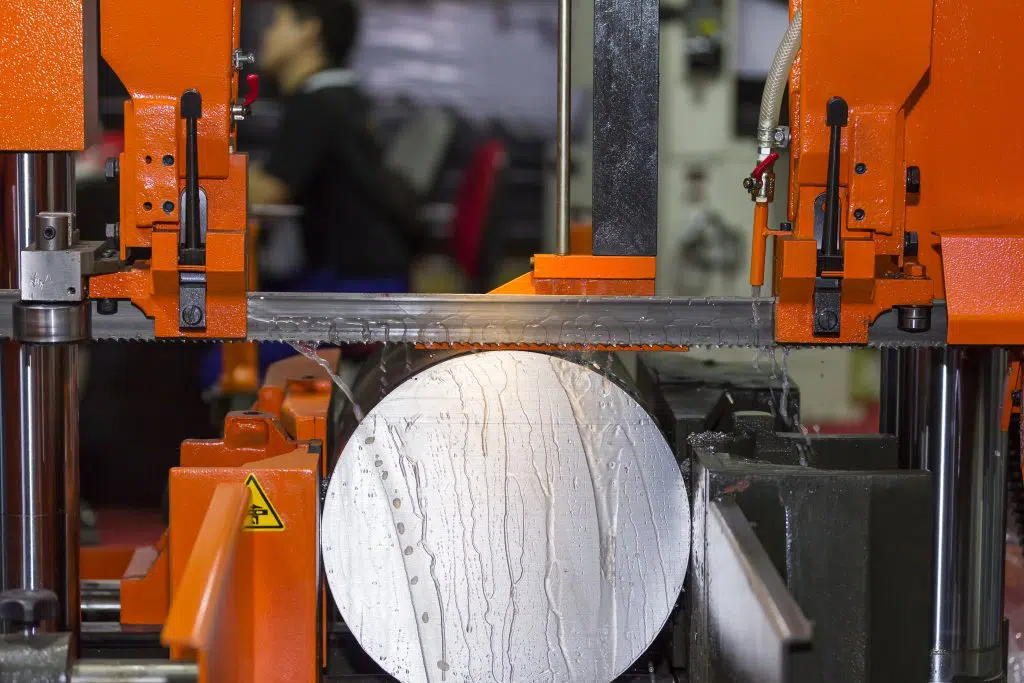
Even the most “normal” cutting operations put an immense amount of pressure on the bandsaw blade that’s doing the cutting. Metal cutting operations take that pressure to the next level. That’s why tougher, more durable metal cutting bandsaw blades like bi-metal and carbide blades are typically used to cut through metal or steel applications. However, no matter the blade or edge type, all metal cutting blades will eventually fail or break just like blades used for less intense applications.
Here are three of the most common reasons behind metal cutting blade breakage.
Bandsaw Misuse
Is your blade properly lubricated to protect against friction? Are you using the right blade or edge type for the type of metal you’re cutting? What is the recommended cutting speed for that particular blade or metal type? These are all questions you or your operator should ask each time you install a new blade on your bandsaw. Fortunately, you can easily negate these issues by thoroughly training all your bandsaw operators.
Improper Blade Tension
The extent to which you tension your metal cutting blades can literally make or break both the blade and your finished product. Over tensioning your blades can lead to hairline cracks along the back edge of the blade and in the gullets of toothed blades. Under tensioning your blades can lead to bowing and premature blade failure.
To combat this, we recommend contacting your bandsaw manufacturer for correct tension settings and measuring blade tension during each installation of a new blade on your bandsaw machinery.
We recently published an entire blog post about the importance of blade tension and the signs of over or under tensioned blades. You may want to check it out if you find yourself frequently encountering this issue.
Incorrect Number of Teeth Per Inch (TPI)
If you want your blades to last, matching the correct number of teeth per inch to the type of metal you’re cutting is imperative. For example, if you’re cutting thin-walled rectangular tubing with a 10 TPI blade, the teeth will usually straddle the thin section and be stripped relatively quickly. However, if your blade has too few TPI, then there may not be enough room in the tooth gullets to pull out chips as the blade makes its way through the material.
No matter the material, at least three teeth should always be engaged in the work (or in contact with the material). Ideally, your blade will have 6-12 teeth engaged in the work though. If you’re having trouble deciding how many TPI your blades you should have, feel free to reference Simmons’ Recommended Tooth Selection for Material chart. It’ll help you get started.
While these are some of the most common reasons metal cutting blades break, they are far from the only reasons. Many cutting operations are unique and so too are the issues they may encounter. Being aware of some common reasons behind blade breakage can put you ahead, but you shouldn’t hesitate to reach out to a blade manufacturer like Simmons should you find yourself stumped by a metal cutting issue.
If you found this article helpful, please let us know in the comments. To learn more about metal cutting bandsaw blades, contact us today!